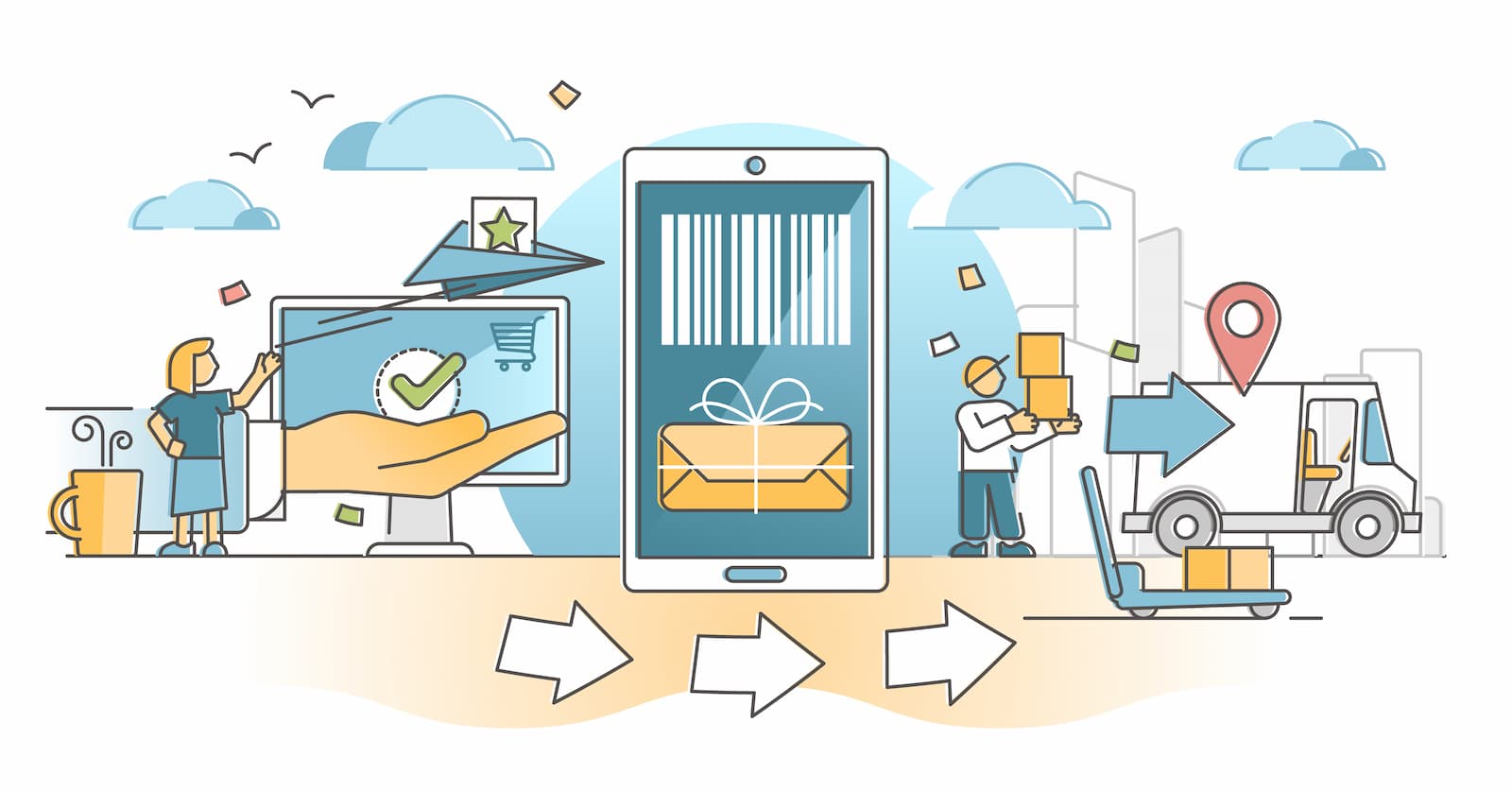
How to Reduce Your Order Fulfillment Time Cycle
Timing is everything. Our world today revolves around technology that has reduced the speed at which information and goods travel across the globe. At the same time, we see heightened expectations of faster order processing, fulfillment, and shipping. So, how can you keep up without sacrificing quality? The goal is to find efficiency within each step of the fulfillment process. Let’s break it down.
What Happens When the Order is Placed?
The customer clicks on “Submit Order” and the clock starts ticking. Ideally, your online ordering system is integrated with your internal inventory and order management programs. If not, you’ll be waiting until an employee can physically transfer order information. A crucial element is communication. Allowing your customers to check the status of their order allows them to get real-time updates and information while keeping your staff free to focus on other tasks.
Keep the Parts Moving
It’s time for your products to start their journey through the warehouse, into shipping, and on their way out the door. Areas to check for efficiency and time-saving include:
– Warehouse location – Be smart about your stock and layouts. Arrange your layout to keep the most used resources close to quality control and shipping. This reduces travel time for pickers and your fulfillment team.
– Technology – Automation can be your friend. Use technology to track inventory in order to prevent stock-outs and prioritize replenishments. After all, you can’t fulfill an order if you don’t have items in stock. An automated pick system can reduce personnel hours needed to traverse through the warehouse and can significantly decrease order fulfillment times. Automation comes in varying degrees of complexity and systems can be designed to fit many needs.
– Personnel – Markets and prices fluctuate and may be beyond your control. Labor costs, however, are completely in your control and should be responsive to your bottom line. Evaluating the numbers and workloads of staff is worth your attention. Do you have enough staff on the floor; are they positioned appropriately? Attracting and retaining staff provides continuity in customer service and company mission. Satisfied employees will produce their best work. Longevity in staff reduces the overhead involved with assimilating new team members.
– Quality Control – automation provides many pieces to an error-free order fulfillment process. But don’t disregard the human touch. Computers recognize data as entered but seasoned staff can recognize anomalies in orders that may prevent an incorrect order from being shipped. Correct orders won’t get returned.
– Shipping – Choose your shipper carefully. A review of your ordering trends will give you insight as to where your customers are; rural, suburban, high-density urban locations. Some shippers won’t deliver to P.O. boxes, others don’t have the capacity to reach remote rural areas. By partnering with multiple carriers, you can increase your reach. Effective negotiations for bulk orders can ensure a daily scheduled pickup time, giving your team a daily target. Negotiated bulk shipping rates allow you to pass on those savings to customers. After all, who doesn’t love free shipping?
Not in Your House?
Sometimes, order fulfillment may rely on outside sources, particularly if you’re working with oversized items that aren’t cost-efficient to warehouse on-site. If you drop ship or use third party inventory, you may be counting on others to satisfy the customer order. In this instance, you become the customer and provider in the same transaction. You’ll want the same transparency and communication with any third party that you strive to provide to your customer. Building solid relationships, great communication, and constant assessment of targets and results with these providers are necessary for success.
Time is money. So the time cycle for your order fulfillment process has a direct impact on company reputation and profits. Small changes can add up to a big difference. A selective combination of automation, personnel, and logistics provides the solution for an efficient, cost-effective strategy. The experts at Tri-R have been providing warehouse storage and racking systems for over 4 decades, and are ready to help you find the right solution for your company.